Titanium alloy has become one of the most promising metal structural materials in the modern aerospace industry due to its excellent combination of low density, high specific strength, high temperature resistance, corrosion resistance and non-magnetic properties. With the large-scale application of titanium alloys, the metallurgical quality problems have attracted more and more attention from the industry, so the metallurgical quality of titanium alloys is becoming more and more important.
At present, more than 80% of industrial titanium alloys are used in the form of deformed titanium alloys, such as forgings, forged bars and rolled profiles. Forging deformation is the most important means to ensure the ideal microstructure and properties of titanium alloy materials, but the incorrect forging process tends to cause some unsatisfactory structural and metallurgical defects in titanium alloy products, thus deteriorating its mechanical properties, giving titanium alloy products The normal use causes potential harm, and at the same time causes a lot of waste for the production and use of the manufacturer. Therefore, it is of great value to study and analyze the formation mechanism of various titanium alloy forging defects and take effective preventive measures.
Forging thermal effect
After a certain grade of high-temperature titanium alloy ingot was forged and forged in a fast forging machine, it was heated and forged into φ 165mm bar in the α+β two-phase zone. After heat treatment, the low-magnification structure was observed as a fuzzy crystal structure, and the microstructure was The equiaxed structure is the ideal α + β duplex titanium alloy equiaxed structure, the photo of which is shown in Figure 1a. After cutting the above-mentioned φ 165mm bar material, it was heated at 50 ° C under the phase change point, and then forged into a φ 110 mm × 110 mm billet on a 30kN hydraulic hammer, and then the core was found to be anatomically analyzed. For clear crystal, the photomicrograph is shown in Figure 1b. The microstructure is α- strip + β- transformation . It is a typical Wei's structure with clear grain boundaries. α belongs to the superheated structure in titanium alloy. The distance from the surface is 20-30mm. Semi-clear crystal, the photomicrograph is shown in Figure 1c, the microstructure is α slat + α isometric + β rotation , the number of α equiaxions is sparse, the number of α slabs is mostly, there is intermittent distribution of grain boundary α; It is a fuzzy crystal in the range of ~20mm.
A certain batch of φ80mm TC4 titanium alloy bar has a typical equiaxed α structure (see Figure 2a), and the initial α equiaxion content is over 70%. After forging at 940 ° C (alloy phase transition point 995 ° C), the microstructure of the die forging part is shown in Fig. 2b, and the initial α equiaxed content is only about 15%, which is caused by overheating of the forging temperature.
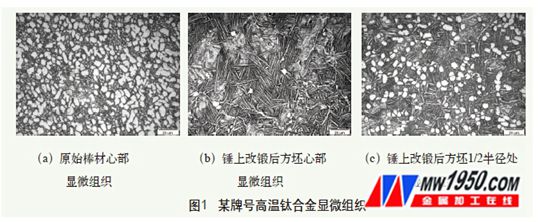
Titanium alloy deformed above the phase transition point (α+β/β transition temperature) to obtain mesh basket structure or Wei's microstructure plasticity and poor fatigue properties, so most of the titanium alloy product technical standards require near α type, α + β type For the finished biphasic titanium alloy, the microstructure is generally an equiaxed structure or a two-state structure with good comprehensive properties. Therefore, the forging of near-α and α+β-type biphasic titanium alloys is generally selected at 30~60 °C below the phase transition point. Heat forging. Great deal of research and engineering practice has proved that with increasing heating temperature of forging, duplex alloy microstructure content equiaxed primary α decreased significantly, while α was significantly increased slats. That duplex alloy upon heating transformation point, as the heating temperature increases, the tissue gradually equiaxed primary α phase transformation to beta], resulting alloy microstructure after hot forging in the equiaxed primary α content decreases, smaller shape, increasing the content of α strip, after hot forging temperature exceeds the transformation point of titanium, titanium alloy bipolar tissue disappeared equiaxed primary α, lath or basketweave Widmanstaten .
The thermal conductivity of titanium is 0.036 cal/cm·s·° C. (1 cal/cm·s·° C. = 418.68 W/cm·K), and is 1/15 of aluminum at room temperature and 1/5 of iron. During the forging process of titanium alloy, due to the large instantaneous deformation rate (7~9m/s on the hammer) and high striking frequency, the internal flow stress of the alloy is too large, and a large amount of mechanical energy is consumed to be converted into internal heat in a short time. around the core portion and the larger deformation and poor heat dissipation, causing the billet internal temperature increases, the maximum degree of deformation temperature close to the central region, and even more than alloy phase transformation, resulting in a sharp reduction in the final microstructure of the blank central equiaxed primary α or even all Disappeared, when the heat is severe, the tissue is transformed into a very poor Wei's tissue. Typical two kinds or more duplex alloy after forging hammer, the microstructure content of the shaft of the primary [alpha], etc. drastically reduced, a corresponding increase in the content of [alpha] lath microstructure changed from ideal as poor equiaxed Wei The main reason for the organization is the overheating of titanium alloy during transient and severe deformation.
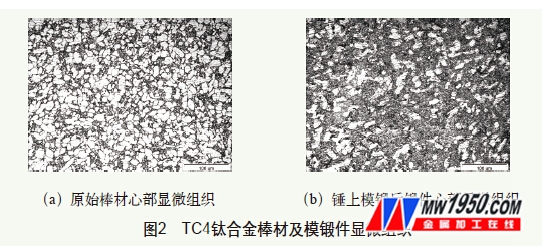
In the forging deformation of titanium alloy, the central part is a severely deformed area in general, so the center is the area with the highest temperature rise, and the temperature rise of the central part is taken as the main basis for formulating the forging process. When forging a titanium alloy with a forging hammer with a faster forging speed, the central thermal effect during the forging process must be considered, and the billet cannot be continuously hit. Forging of titanium alloys is recommended under the condition of a press or fast forging machine. The forging speed of such forging equipment is low, the instantaneous strain rate of the blank during the forging process is low, the deformation heat generated is not very obvious, and there is enough time for deformation. Thermal diffusion does not cause a significant increase in the instantaneous core temperature.
2. Uneven organization
When a batch of T C17 titanium alloy die forgings was observed for microstructure, it was found that there was a certain large block α phase (commonly known as coarse α block) in the basket structure. The TC17 titanium alloy die forging is produced by the sub-β forging process (40 °C heating die forging at the phase change point, air cooling after forging), and it is expected that the microstructure is uniform and uniform.
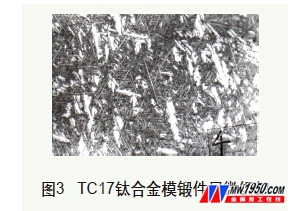
This coarse α block is also called a large white block. Compared with the fine normal α strip in the basket structure, it is coarse and uneven in morphology, and grows from grain boundary to crystal. The interlacing phenomenon rarely occurs. It is rough and uneven, while the crystal interface of the normal α strip is relatively smooth. Studies have shown that the micro-hardness of this coarse α block is about 10% lower than that of the normal α strip, which causes the plasticity and thermal stability of the alloy to decrease, which affects the quality of the forging, so it is necessary to prevent such uneven structure from occurring in the titanium alloy. In the process of smelting and solidification of titanium alloy, due to the equilibrium distribution coefficient ≠1 of various alloying elements, α-stabilized elements are enriched and segregated at the grain boundary of post-solidification, so the α phase first precipitates and crystallizes at the enrichment point. The boundary grows into the crystal, thereby forming a large α block, and the segregation of the micro-area component is the root cause of such uneven structure.
The crystal segregation of the micro-components is caused by the equilibrium partition coefficient k 0 >1 or k 0 <1. The segregation formed by the different solute concentrations in the successive crystalline regions of the alloy is normal segregation. This segregation is difficult to avoid completely, but can be controlled by appropriate measures. . On the one hand, it is controlled by improving the optimization of the ingot smelting process parameters, and on the other hand, it is improved and eliminated by a suitable forging process. For the forging process, firstly, in the forging of the ingot, the appropriate high-temperature homogenization treatment is adopted, and the microscopic intragranular dendrite segregation in the columnar microstructure region of the ingot is improved and eliminated by homogenization annealing or deformation recrystallization; secondly in the alloy The blank and the finished die forging process are controlled by appropriate forging and cooling methods to suppress the occurrence of coarse α blocks in the microstructure. After the above-mentioned β-die forging, the above-mentioned TC17 titanium alloy forging is the cause of the occurrence of coarse α block. The cooling rate after forging is slow, the degree of subcooling is small, and the nucleation rate is low. Therefore, the α phase has enough time to grow to form coarse α. Piece.
Sub-β forging using rapid cooling (water-cooling or oil-cooling) can significantly reduce or inhibit the appearance of coarse α blocks, accelerate the cooling rate, increase the degree of subcooling, and increase the nucleation rate of the α phase, although there are alloying elements in the local area, which have growth. The condition of the coarse α block, but the α phase has not yet reached the growth and merger, the phase transition process of the whole organization has ended, and the control of the cooling rate can significantly change the morphology and distribution of the precipitated α phase. Water-cooling or oil-cooling after forging fixes all or part of the crystal defects (dislocations, subgrains) and dislocation density-enhanced deformation structures to room temperature, and adds a large number of crystal cores for recrystallization during subsequent heat treatment. During the heat treatment, the precipitation mechanism of the β phase changes from the induced nucleation mechanism under air-cooling conditions to the independent nucleation method, resulting in small, chaotic, interlaced strips of primary α and secondary α, which can significantly improve the alloy synthesis. performance.
3. Cavity defects
A batch of φ 70mm-size TA7 titanium alloy bar was found to have exceeded the standard defect wave at the factory ultrasonic inspection. After the defect position was dissected, the horizontal low-spectrum inspection was carried out. After the corrosion, a large number of “pit pits†were found at low magnification, mainly concentrated on In the center of the bar, no area was found in the area outside the 1/4 radius of the bar. Subsequently, a high magnification observation was made on the pit, and it was found to be an intercrystalline void defect. The photomicrograph of the defect is shown in Fig. 4. Some studies believe that the phenomenon of "ma-pit" is related to corrosion. With the increase of corrosion time, the phenomenon of "pit pit" is more obvious. Some studies believe that "ma-pit" may be related to the content of impurity element Fe. However, the above viewpoints are difficult to explain the phenomenon that ultrasonic detection has excessive defect waves and the void phenomenon found in high-power analysis.
A large number of engineering practices have proved that the performance of TA7 forging process is worse than other titanium alloys such as TC4 and TC11. The forging process is more prone to cracking than other titanium alloys, and the crack growth rate is fast. Metal materials such as titanium and aluminum alloys are prone to loosening when large strains (such as superplastic forming) occur, and voids or even fractures occur. The hollow hole of TA7 titanium alloy is induced by large strain. At high strain rate, the flow stress of TA7 titanium alloy increases significantly compared with static, but the plasticity decreases significantly. As the strain rate increases, the flow stress strain increases, but there is a critical strain rate. When the critical value is exceeded, the material will occur. When the strain rate reaches a critical value, an adiabatic shear band is generated in the material, and microvoids are formed in the band. Under the action of external stress, the cavity gradually aggregates and grows even to form microcracks. Microvoids are always formed along the maximum shear band. This is because in the localized deformation, the deformation in the maximum shear band is severe and the temperature is high, which softens the material inside the band and becomes an ideal place for defects such as cracks and voids. In the forging process, the TA7 bar has the largest deformation amount in the center of the bar and the slowest deformation heat diffusion, and the deformation temperature is the highest, so the cavity is most likely to occur during the large deformation process.
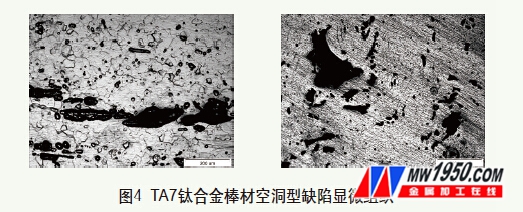
Studies have shown that the plastic deformation process of metal materials is accompanied by changes in microstructure, mainly grain growth, equiaxed crystal elongation, grain rotation and sliding, dislocation proliferation, dynamic recovery and recrystallization, and void nucleation and length. Great. Grain boundary slip is the main mechanism of plastic deformation. Grain boundary slip will cause local stress concentration and hinder the further occurrence of grain boundary slip. When stress concentration cannot be eliminated by dislocation motion, the cavity will be nucleated and then grow. Big. The void preferentially nucleates at the triangular grain boundary. As the amount of deformation increases, the cavity begins to grow, and the cavity does not grow in an equiaxed state, but grows in an elliptical manner. The voids tend to diffuse to the grain boundary shared by the parallel tensile stress, thereby forming a directional vacancy flow in the direction of the tensile stress, continuously accumulating toward the center of the cavity, so that the cavity grows parallel to the stretching direction. A large number of references have mentioned that the "pitting" and voids are prone to occur in the forging process of the alloy. Through the analysis of the "pitting" of TA7 titanium alloy and the formation mechanism of void-like defects, we have concluded a set of cavities for preventing the toughness of TA7 titanium alloy forgings. The effective method is to strictly control the deformation amount per fire ≤ 50%, strictly control the deformation rate, preferably by hydraulic press or hydraulic press forging, try to avoid hammer forging, and achieved good results in production.
4. Conclusion
At present, the common forging defects in titanium alloy mainly include microstructure overheating and unevenness, voids, cracks, etc. These defects are generally found in the microstructure inspection or ultrasonic inspection of titanium alloy products, mainly in the process of titanium alloy product forging. If the parameter control is improperly formed, it is necessary to select a suitable deformation rate (forging equipment), heating forging temperature, pass deformation amount and post-forging cooling speed according to different characteristics of the titanium alloy material in the forging process.
About the author: Zhang Lijun, Guo Kai, Zhang Chenhui, Xi'an Xigongda Chaojing Technology Development Co., Ltd.
He Chunyan, Quality Management Department of Western Titanium Industry Co., Ltd.
Xue Xiangyi, State Key Laboratory of Solidification Technology, Northwestern Polytechnical University.
Bath Taps
Our range of bath taps and mixers are available in a gorgeous choice of designs. Choose from a range of contemporary or traditional Basin Taps or bath taps, or if you are looking for something a little more modern, select from our range of deck mounted or wall mounted basin and bath mixers which deliver water through a single spout. For the ultimate flexibility, also take a look at our range of bath shower mixers. Our bath taps and mixers combine exceptional quality design with real value for money. Selected products in the range also include clever flow limiting devices to help save water. Taps with lever handles have also been designed to be easy to use and some of our ranges are suitable for low pressure.
Bathroom Basin Taps, Bath Mixer Taps, Shower Bath Taps, Stainless Steel Bath Taps
ZHEJIANG KINGSIR VALVE CO., LTD. , https://www.kingsir-valve.com